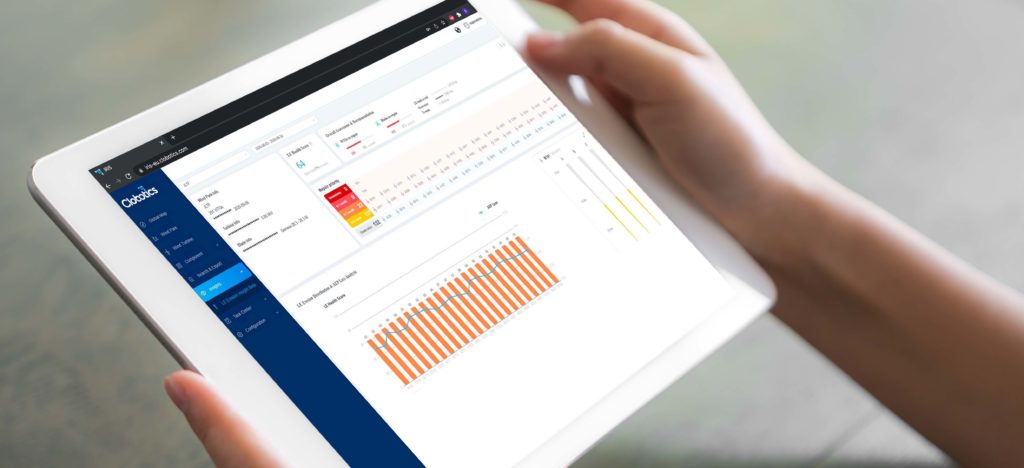
Data Management
Data is collected throughout the lifespan of a wind turbine. This inspection data is a valuable source of information that is used for planning maintenance and repairs but also for evidence as part of a change in ownership and service responsibility.
Clobotics IRIS™ enables customers to generate a fast overview but also dig deep down to one specific defect. From there, the customer can append comments and recommendations to suppliers and other stakeholders.
IRIS™ also supports upload of legacy data via structured image folders and a standard Excel file format for the metadata. And IRIS™ customers can set up accounts in the system to allow techs, engineers and other collaborators to access the data with flexible permissions based on their role.
To minimize our carbon footprint, our data centres have been chosen for their energy efficiency – all have a DCiE (Data Center Infrastructure Efficiency) of 83% or higher.
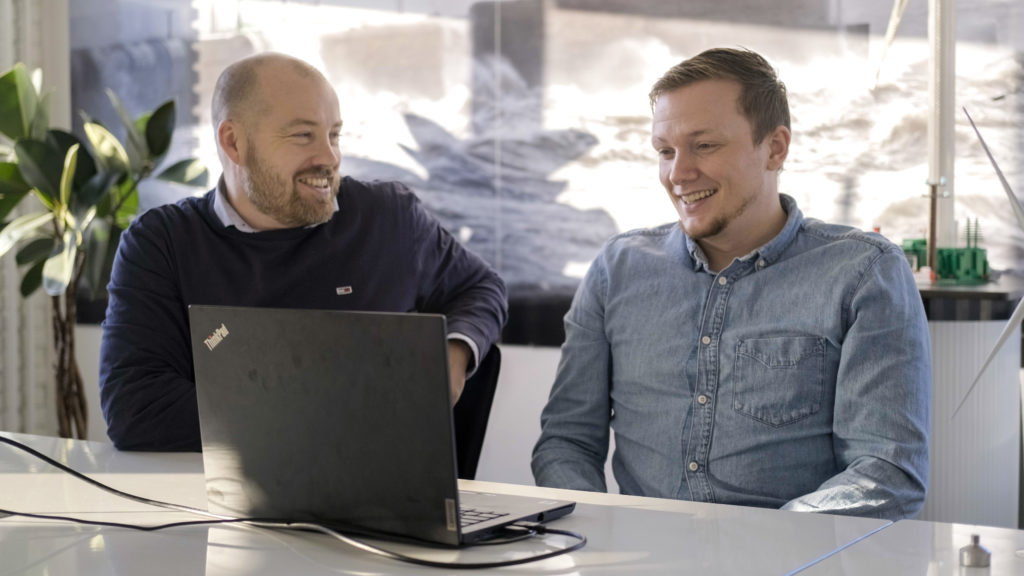
Change to IRIS™ with ease
When changing your data handling to IRIS™ you will be assisted with training and support from your local region. Clobotics operates globally and has the possibility to offer support in all time zones as needed.
IRIS™ is an intuitive online portal where no apps or downloads are needed. You will be granted a username and password and you have instant access to all your data.
Clobotics IRIS™ has been engineered to upload various forms of drone and camera inspection data. If the information is consistent and in the most common formats, we can upload it and generate statistical overviews for use in planning. Data in special formats can be analyzed for the possibility of a custom upload.
Our software engineers continuously improve our portal with the goal of being the preferred tool for managing blades, tower, and foundation inspections.
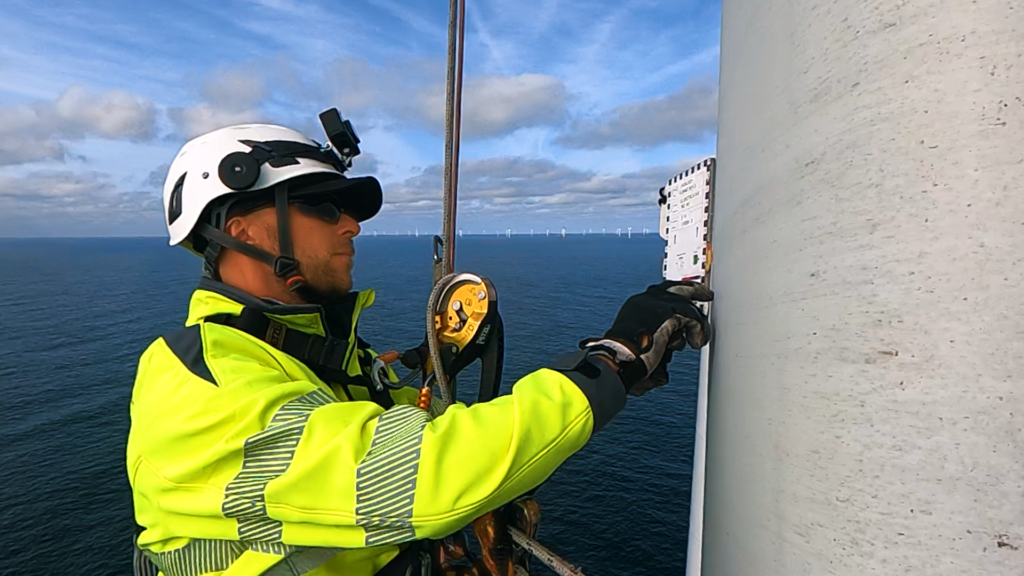
Repair Tracking with Raven Technologies (EMEA only)
Raven consists of hardware for collecting data and a software package for finalizing repair or inspection reports. After each day, the data is submitted to the Raven online portal where our blade specialist can oversee the quality of repairs and documentation. The data can also be accessed online by our clients that can closely follow the progress of our field work.
Raven optimizes the workflow of repair technicians and ensures that all repair steps are being captured automatically. Raven produces accurate data for reporting and the results are presented online with easy access.
Blade repairs are often expensive due to complicated logistics and working windows are often short because of weather conditions. Raven ensures full traceability for all environmental data, curing times and material batch numbers being used.