From the minute they appeared, camera drones joined the arsenal of tools which enterprising site operators use to figure out what’s going on with their wind turbine blades. And for good reason.
Buying an off-the-shelf camera drone has become less expensive over time, becoming an expense more easily afforded within existing budgets. A “Do-It-Yourself” (DIY) approach using a drone owned on-site provides the highest flexibility to inspect when convenient, without the time and dollar cost of mobilizing a 3rd party to the site. And, as the drone cameras have improved, the quality of the images has gotten better and better
So, maybe DIY is good enough when it comes to doing visual blade inspections?
There are three reasons why we believe our investments to create an end-to-end, fully automated, and purpose-built system for doing this critical job will pay off for our customers.
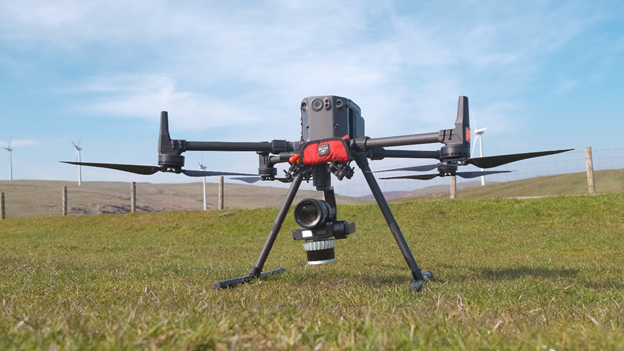
Reason #1: Image Quality
The quality of images collected will be higher even if the resolution of the cameras is the same.
Maintaining a constant distance and angle to the blade is very difficult, especially for blades at an angle to the ground. Constant distance eliminates the need to change focus and accurate angles are important for calculating the size of anomalies that show up in the analysis phase. Controlling these things while flying manually is quite difficult, but our Clobotics IBIS™ automates that process.
Complete coverage is another important quality metric. Our automation allows the pilot to see a stitched composite of all the images collected for each blade immediately after landing, making it very easy to confirm that the inspection has captured all blade surfaces.

Reason #2: Image Analysis
This quality can make a big difference when it comes time to analyze the images to determine what’s going on or to take action, such as getting quotes for repairs.
We spoke to a repair company, who told us that the difference between being able to quote fixed-price jobs (where they take the risk) versus time and materials (where the owner does) can often come down to the quality of the images available and the report quality.
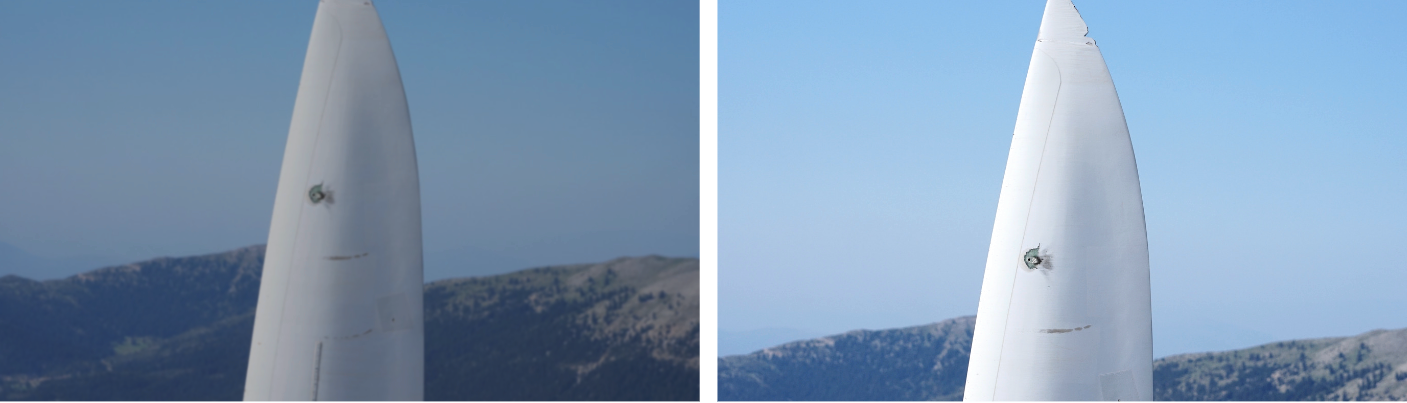
Reason #3: Consistency
As important as the quality is, the consistency of the data collected. Inspections conducted manually, or semi-manually, will not yield the consistency of data that a fully autonomous system does.
While this may not matter much for a one-off inspection, it matters a lot when you are planning a data-driven O&M system that needs to work across sites and over time.
Suppose the goal is a system that “turns sight into insight” fleetwide by automatically collecting and analyzing visual images of blades to generate recommended maintenance and repair actions. In that case, that system must sit on a foundation of consistently captured, high-quality data to realize its potential.
We have enabled the best of both worlds by investing in full automation.
Drone as a Service
Our technology is straightforward enough to be operated by technicians with drone flying experience and minimal additional training.
So, our customers can utilize their personnel and get the flexibility of DIY but retain the consistency and quality of data capture needed to enable a world-class vision-based inspection and maintenance program for their blades.
In summary, DIY inspections using off-the-shelf drones is a low-cost, flexible way to accomplish one-off inspections as their need arises. But a fleetwide system for managing blades should rest on a foundation of consistent, high-quality image data capture. Clobotics Drone as a Service offering enables consistent, high-quality capture with the flexibility of using existing personnel and avoiding mobilization of third parties to the site.
Sidebar on Image Quality
Automation provides numerous benefits to image quality as shown below:
Resolution: even if the camera resolutions are the same between a manual and autonomous system, the manual operator will often need to fly further from the blade to ensure safe operation, resulting in lower effective resolution of the images taken.
Motion Blur can occur if camera settings are incorrect or drone speed gets too high. Clobotics IBIS™ precisely controls these parameters throughout the inspection.
Pitch angle is critical to enabling accurate assessment of damages in the analysis phase. Manual inspections often result in images featuring difficult pitch angles whereas Clobotics IBIS™ ensures a consistent 90 degree angle to the blade surface being photographed.
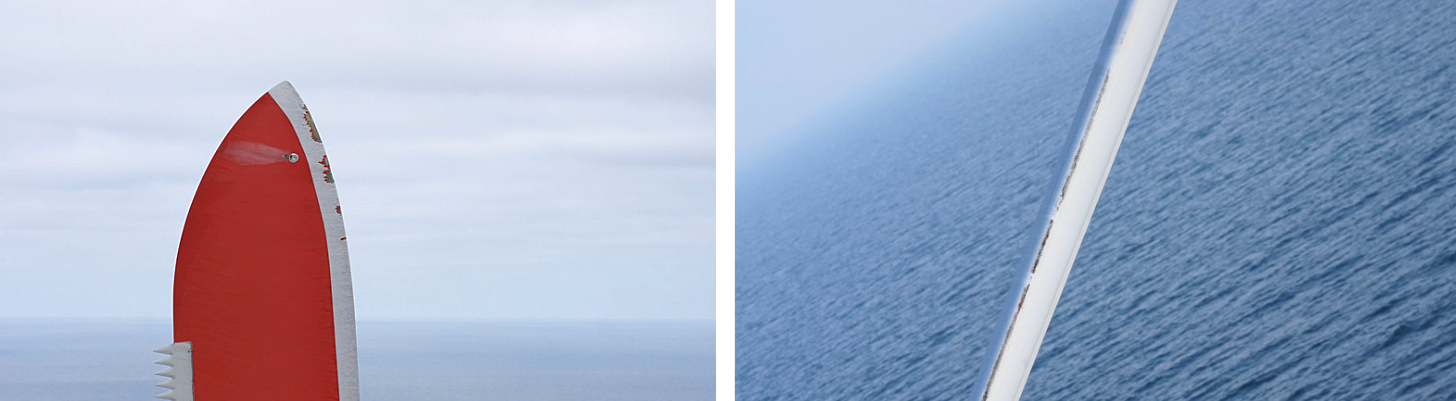
Rogers Weed is the Managing Director, Americas at Clobotics Wind Services.
Other Point of View Articles:
- The case for open standards around blade inspections
- Making the case for more frequent blade inspections